In the realm of electronic component testing, the SMD5 series chip sockets present a unique set of challenges due to their large size and high current capabilities, exceeding 40A of current rating. These sockets are critical components in modern electronic assemblies, particularly in automotive applications where stringent testing requirements must be met to ensure reliability and safety standards are upheld.
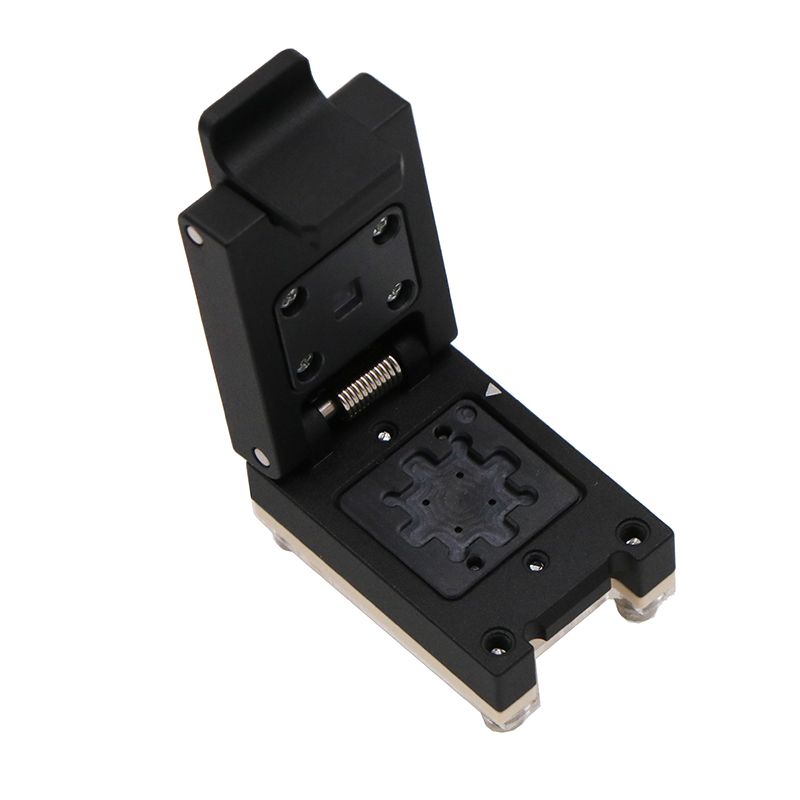
Importance of Testing
The significance of testing SMD5 series chip sockets cannot be overstated, especially in automotive contexts where the reliability of electronic components directly impacts vehicle performance and safety. Key aspects highlighting the importance include:
- Reliability Assurance: Automotive environments subject electronic components to harsh conditions such as temperature extremes, vibration, and moisture. Testing ensures that SMD5 chip sockets can withstand these challenges without performance degradation or failure.
- Safety Compliance: Vehicles adhere to strict regulatory standards (e.g., ISO 16750) mandating the reliability and durability of electronic components. Testing validates that SMD5 sockets meet these requirements, preventing potential safety hazards.
- Cost Efficiency: Early detection of faults through rigorous testing reduces the likelihood of expensive recalls and repairs. This proactive approach enhances cost efficiency in automotive manufacturing and maintenance.
Challenges in Testing
Testing SMD5 series chip sockets poses significant technical hurdles due to their unique characteristics:
- High Current Handling: With current ratings exceeding 40A, ensuring accurate measurement and verification of current carrying capabilities without overheating or damage during testing is paramount.
- Mechanical Durability: The sockets must endure repeated insertions and removals without compromising mechanical integrity. Testing evaluates resilience against physical wear and tear to guarantee long-term reliability.
- Contact Resistance: Maintaining low contact resistance is critical to prevent power loss and heat generation, which can affect performance and efficiency. Testing verifies consistent electrical connectivity under varying conditions.
- Environmental Simulation: Simulating automotive operational conditions (e.g., temperature cycling, humidity) during testing is essential to assess performance under real-world scenarios and ensure reliability over the vehicle’s lifespan.
Testing Methodologies
To address these challenges effectively, advanced testing methodologies are employed:
- Current Carrying Capacity Tests: Conducted to validate the socket’s ability to handle specified currents without exceeding temperature limits or compromising electrical integrity.
- Mechanical Endurance Tests: Evaluate the socket’s durability through repeated insertions and extractions to simulate real-world usage conditions.
- Environmental Stress Screening (ESS): Subjects the sockets to temperature extremes, thermal cycling, and humidity variations to identify potential weaknesses and ensure robustness in diverse operating environments.
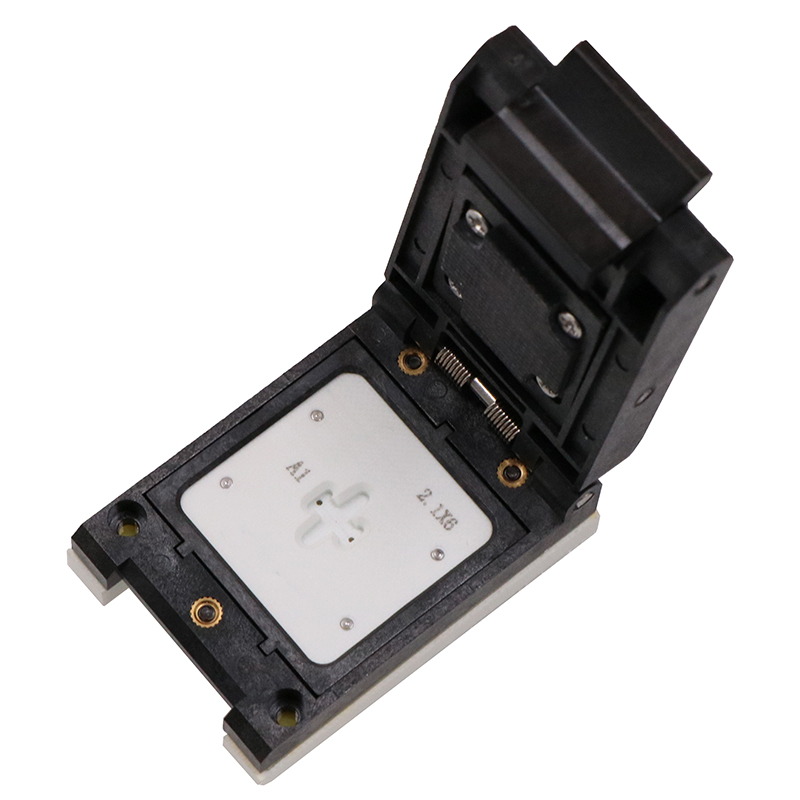
发表回复