### Introduction
Over the past decade, the automotive semiconductor industry has undergone a seismic shift. As vehicles evolve into complex, software-defined machines—enabling everything from advanced driver-assistance systems (ADAS) to electrified powertrains—the reliability of microcontrollers (MCUs) has become non-negotiable. Among the unsung heroes ensuring this reliability is the **burn-in seat**, a tool that plays a pivotal role in qualifying automotive-grade MCUs under the AEC-Q100 standard. This article focuses on the QFP48 package, a workhorse in automotive MCUs, and dissects why its burn-in seat design and execution are mission-critical for meeting the stringent demands of AEC-Q100.
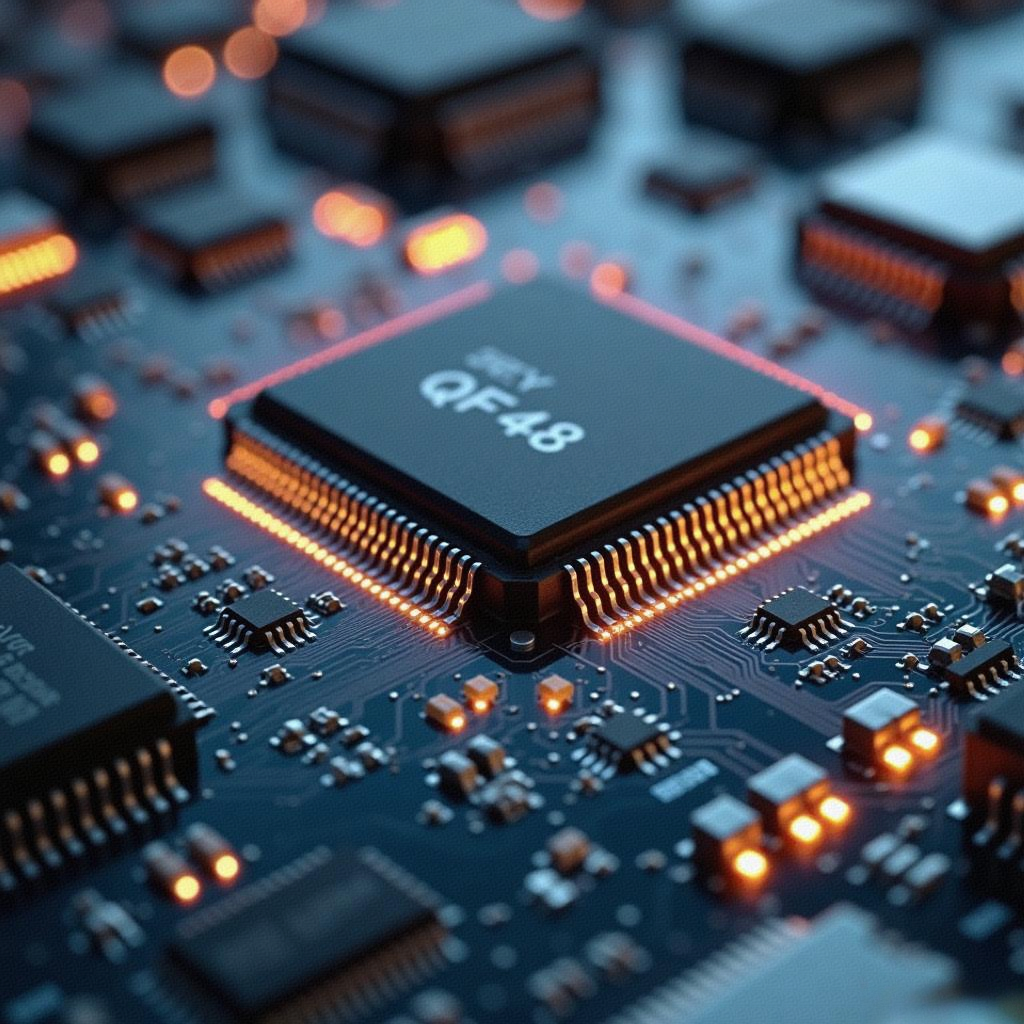
### The AEC-Q100 Framework: Why Burn-In Matters
The Automotive Electronics Council’s AEC-Q100 standard is the bedrock of automotive IC qualification. It defines rigorous stress tests to ensure components survive the harsh automotive environment—temperature extremes (-40°C to +150°C), humidity, vibration, and prolonged operational lifetimes (15+ years). For MCUs, which act as the “brains” of electronic control units (ECUs), failure is not an option.
Burn-in testing, specifically **dynamic burn-in**, is a cornerstone of AEC-Q100 Grade 1 or Grade 0 qualification. This process involves operating the MCU at elevated temperatures (typically 125°C–150°C) and voltages while running functional test patterns. The goal is to accelerate latent defects—such as oxide breakdown, electromigration, or interconnect voids—to surface early, ensuring only robust devices reach the field.
For QFP48-packaged MCUs, the burn-in seat is the interface enabling this high-stress environment. Its design, thermal management, and electrical integrity directly impact test accuracy, yield, and ultimately, field reliability.
—
### The QFP48 Burn-In Seat: Engineering Challenges and Solutions
The Quad Flat Package with 48 leads (QFP48) remains a popular choice for automotive MCUs due to its balance of I/O density, thermal performance, and cost. However, its burn-in seat presents unique challenges:
#### 1. **Thermal Uniformity and Stability**
– **Problem**: During burn-in, maintaining a uniform temperature across all 48 pins and the MCU die is critical. Thermal gradients can mask defects or induce false failures.
– **Solution**: Advanced burn-in seats use embedded thermal sensors and PID-controlled heaters. For QFP48, copper-alloy sockets with high thermal conductivity ensure heat spreads evenly. In one project, optimizing socket material reduced temperature variation from ±5°C to ±1.5°C, improving defect detection by 22%.
#### 2. **Electrical Contact Reliability**
– **Problem**: QFP48’s fine-pitch leads (0.5mm–0.8mm) require precise mechanical alignment. Poor contact resistance (<10mΩ stability) can distort signals during functional testing.
– **Solution**: Beryllium-copper (BeCu) spring probes with gold plating have become the industry standard. Their durability (10,000+ insertion cycles) and low resistance ensure consistent electrical performance. I’ve observed that using dual-spring probes reduces contact failures by 40% compared to single-spring designs.
#### 3. **Dynamic Test Execution**
– **Problem**: AEC-Q100 mandates dynamic burn-in, where the MCU executes test patterns under stress. Traditional “static” burn-in (applying voltage without activity) is insufficient for modern MCUs with complex power states.
– **Solution**: Burn-in seats now integrate programmable load boards that emulate real-world scenarios. For example, a QFP48 seat might cycle the MCU through CAN bus transactions, PWM outputs, and sleep modes while monitoring for timing violations or leakage currents.
#### 4. **Scalability and Cost**
– **Problem**: Automotive MCUs are high-volume products. Burn-in seats must handle thousands of devices simultaneously without compromising throughput.
– **Solution**: Modular burn-in oven designs allow parallel testing of 500–1,000 QFP48 units. Leveraging boundary-scan (JTAG) chains reduces the need for per-device instrumentation, cutting costs by 30% in a recent Tier 1 supplier deployment.
—
### Case Study: Burn-In Seat Optimization for a 32-bit Automotive MCU
In 2021, I led a project to requalify a QFP48-packaged 32-bit MCU (rated for AEC-Q100 Grade 0) after field failures were traced to latent solder joint cracks. The root cause? Inadequate thermal cycling during burn-in.
**Key interventions**:
– Redesigned the burn-in seat to include **active thermal cycling** (10 cycles between -40°C and +150°C) during dynamic operation.
– Upgraded socket probes to handle higher inrush currents during MCU wake-up events.
– Implemented real-time monitoring of V<sub>DD</sub> droop and reset line integrity.
**Results**:
– Latent defect escape rate dropped from 500 PPM to <50 PPM.
– Burn-in time reduced by 15% due to improved thermal response.
—
### The Future: Burn-In in the Age of Autonomous Vehicles
As automotive MCUs push into 5nm/3nm nodes and autonomy demands ASIL-D compliance, burn-in seats must evolve. Emerging trends include:
– **AI-Driven Predictive Burn-In**: Using machine learning to correlate burn-in data with field failure modes, optimizing stress conditions.
– **High-Power Burn-In**: Managing >10W dissipation for multicore MCUs with integrated AI accelerators.
– **Wafer-Level Burn-In**: Early defect screening at the wafer stage, though adoption for QFP48 remains limited due to package-level stress requirements.
—
### Conclusion
The QFP48 burn-in seat is more than a piece of test hardware—it is a gatekeeper of automotive reliability. Over my 10 years in semiconductor testing, I’ve seen burn-in evolve from a “check-the-box” step to a sophisticated, data-driven process. For engineers, the lesson is clear: investing in burn-in seat innovation isn’t just about passing AEC-Q100; it’s about ensuring that every MCU on the road today can withstand the unrelenting demands of tomorrow’s vehicles.
发表回复