In the semiconductor industry, burn-in testing is a critical process used to identify early failures in integrated circuits (ICs) by subjecting them to elevated temperatures and electrical stress. The burn-in socket, which serves as the interface between the IC and the test equipment, plays a pivotal role in ensuring the accuracy and reliability of this process. As a semiconductor test engineer with over a decade of experience, I have witnessed the evolution of burn-in socket materials and their impact on high-temperature testing. This article delves into the key considerations for material selection in advanced burn-in sockets, particularly for high-temperature applications.
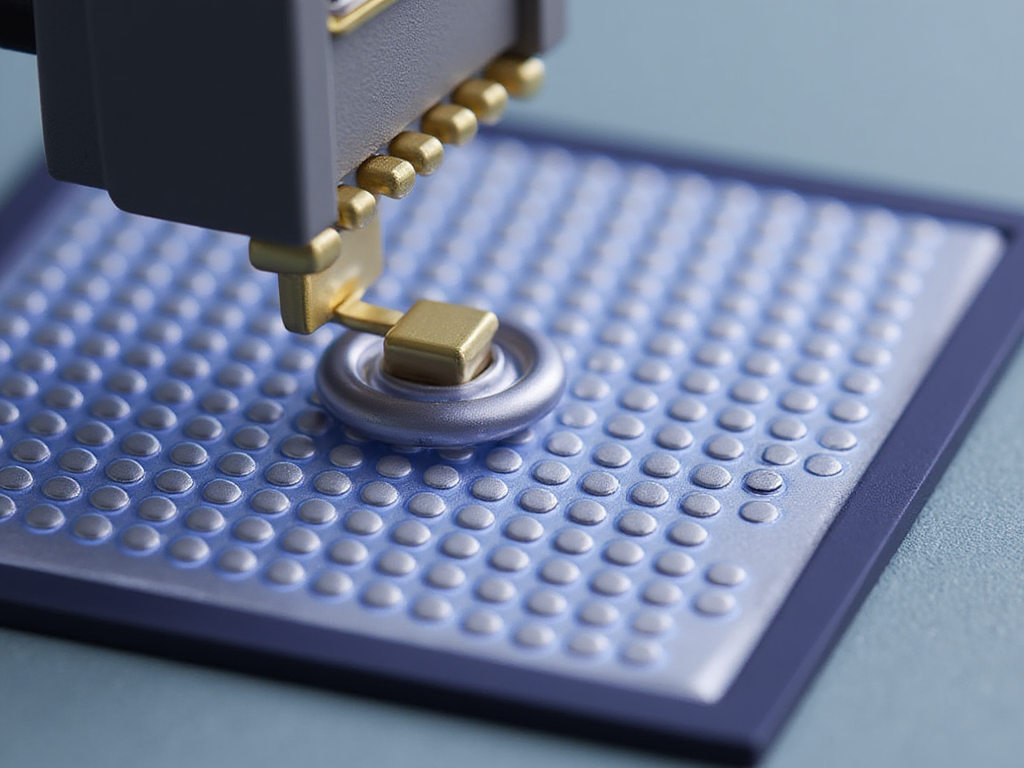
### 1. **Thermal Stability and Conductivity**
One of the primary challenges in high-temperature burn-in testing is maintaining the thermal stability of the socket materials. The materials must withstand prolonged exposure to temperatures often exceeding 150°C without degrading. High thermal conductivity is equally important to ensure efficient heat dissipation from the IC to the socket, preventing localized hotspots that could lead to premature device failure.
Materials such as beryllium copper (BeCu) and phosphor bronze are commonly used for socket contacts due to their excellent thermal conductivity and mechanical properties. However, for the socket body, high-temperature thermoplastics like polyether ether ketone (PEEK) and liquid crystal polymers (LCP) are preferred. These materials offer superior thermal stability and can maintain their structural integrity under extreme conditions.
### 2. **Mechanical Durability and Contact Reliability**
The mechanical durability of burn-in socket materials is crucial, especially in high-temperature environments where thermal expansion can lead to material fatigue. The socket must maintain consistent contact pressure and alignment with the IC pins throughout the testing cycle. Any deviation can result in intermittent connections, leading to inaccurate test results.
BeCu is widely used for socket contacts due to its high strength and elasticity, which ensure reliable contact even after thousands of insertion and extraction cycles. For the socket body, materials with low coefficients of thermal expansion (CTE) are essential to minimize dimensional changes during temperature fluctuations. Advanced composites and ceramics are increasingly being explored for their ability to provide both mechanical durability and thermal stability.
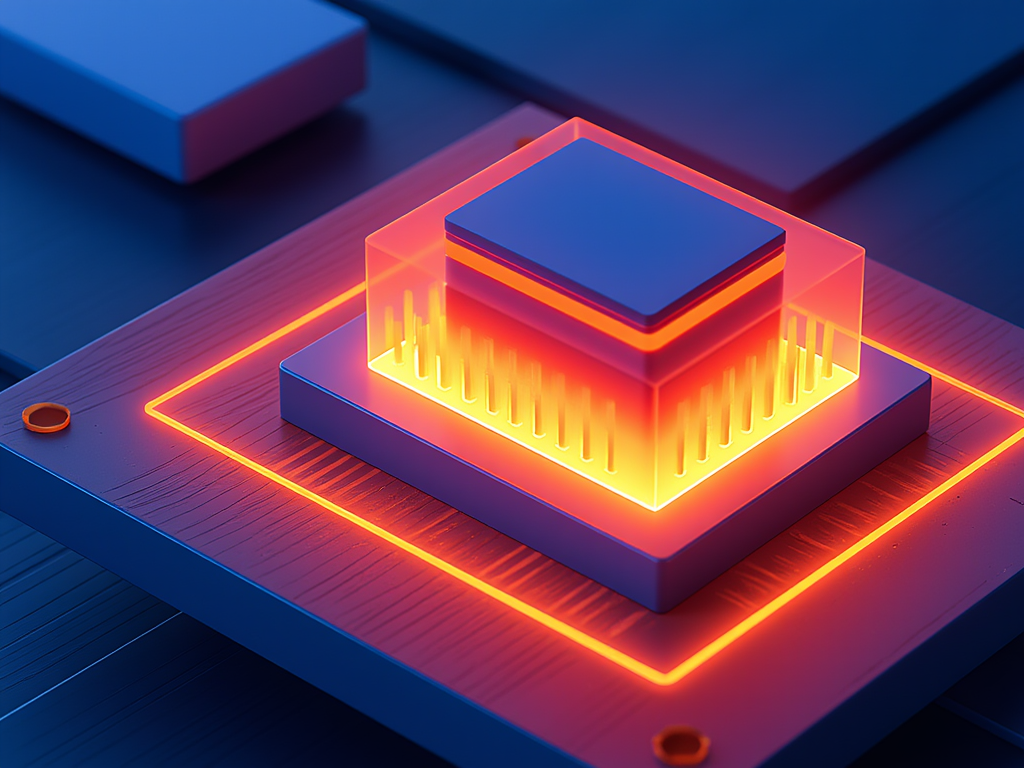
### 3. **Electrical Performance**
Electrical performance is another critical factor in material selection for burn-in sockets. The materials must exhibit low electrical resistance to ensure accurate signal transmission between the IC and the test equipment. Additionally, they should have excellent insulation properties to prevent electrical leakage or short circuits, especially at high temperatures.
BeCu and phosphor bronze are favored for their low electrical resistance, while high-temperature thermoplastics like PEEK and LCP provide excellent insulation. The combination of these materials ensures that the socket can deliver reliable electrical performance throughout the burn-in process.
### 4. **Chemical Resistance and Cleanliness**
High-temperature burn-in testing often involves exposure to various chemicals, including fluxes, cleaning agents, and other process materials. The socket materials must be resistant to chemical degradation to maintain their performance and longevity. Additionally, the materials should not outgas or release contaminants that could affect the IC or the testing environment.
PEEK and LCP are known for their chemical resistance and low outgassing properties, making them ideal choices for burn-in socket bodies. For contacts, materials like gold-plated BeCu are used to enhance corrosion resistance and ensure long-term reliability.
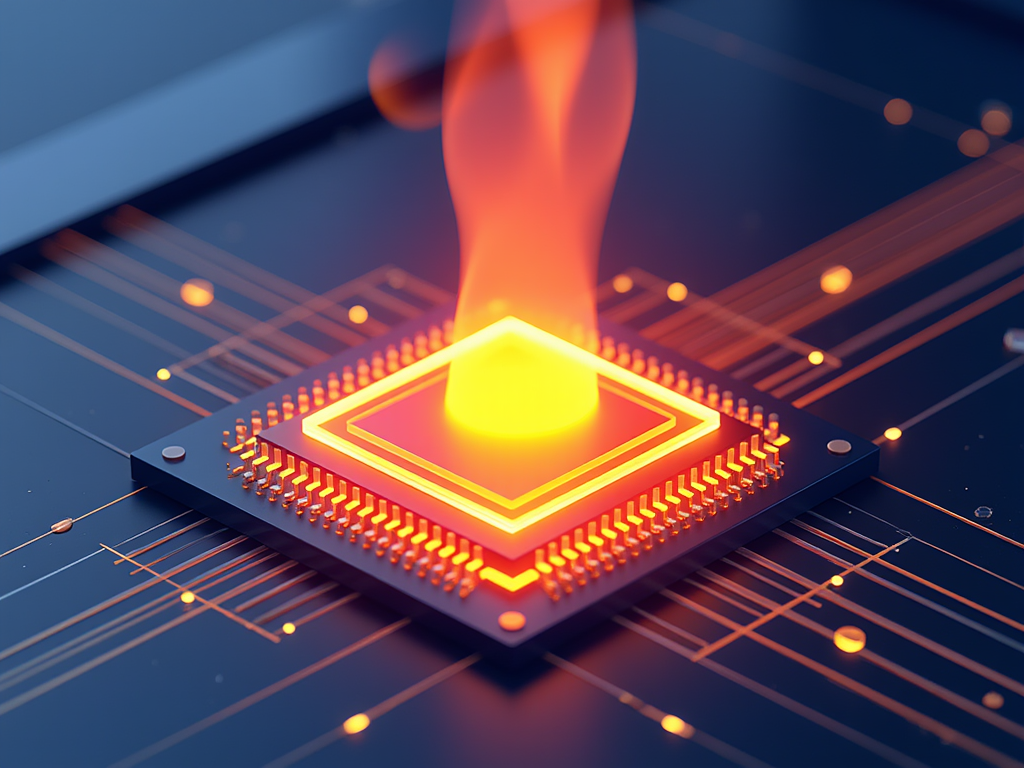
### 5. **Cost and Manufacturability**
While performance is paramount, cost and manufacturability are also important considerations in material selection. Advanced materials like PEEK and LCP, while offering superior properties, can be more expensive than traditional plastics. However, the long-term benefits in terms of reliability and reduced maintenance often justify the initial investment.
Manufacturability is another factor to consider. The materials must be compatible with existing manufacturing processes, such as injection molding and precision machining, to ensure consistent quality and cost-effective production.
### Conclusion
The selection of materials for advanced burn-in sockets in high-temperature testing is a complex process that requires a careful balance of thermal stability, mechanical durability, electrical performance, chemical resistance, and cost. As semiconductor devices continue to evolve, the demand for more robust and reliable burn-in sockets will only increase. By leveraging advanced materials and innovative design techniques, we can meet these challenges and ensure the continued success of high-temperature burn-in testing in the semiconductor industry.
发表回复