1. Signal Integrity
- Characteristic Impedance Control: In high-frequency applications, the characteristic impedance of the PCB needs to be precisely controlled to avoid signal reflections and crosstalk. High-quality PCB manufacturing can ensure consistent impedance, thereby improving the accuracy of test data.
- Inter-layer Connections: In multi-layer PCBs, good coupling between signal lines and ground planes can effectively reduce electromagnetic interference (EMI), ensuring clarity of signals during testing.
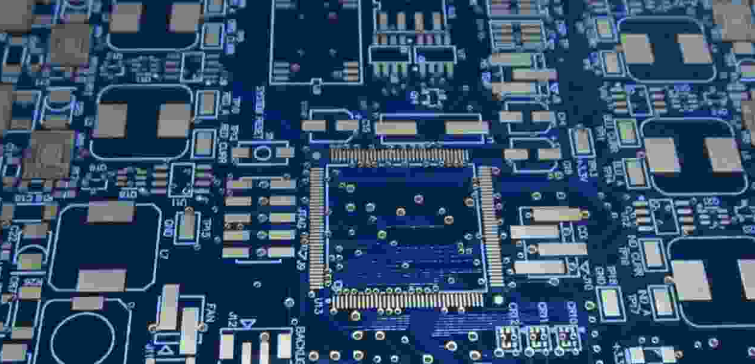
2. Mechanical Stability
- Material Selection: High-quality PCB materials (such as FR-4, polyimide, etc.) have better temperature and moisture resistance, capable of withstanding multiple insertions without deformation, ensuring reliability of the test socket.
- Thickness Control: The thickness of the PCB directly affects the compatibility of the test socket; strict thickness tolerances can ensure good contact between the test socket and the PCB, avoiding test failures due to poor connections.
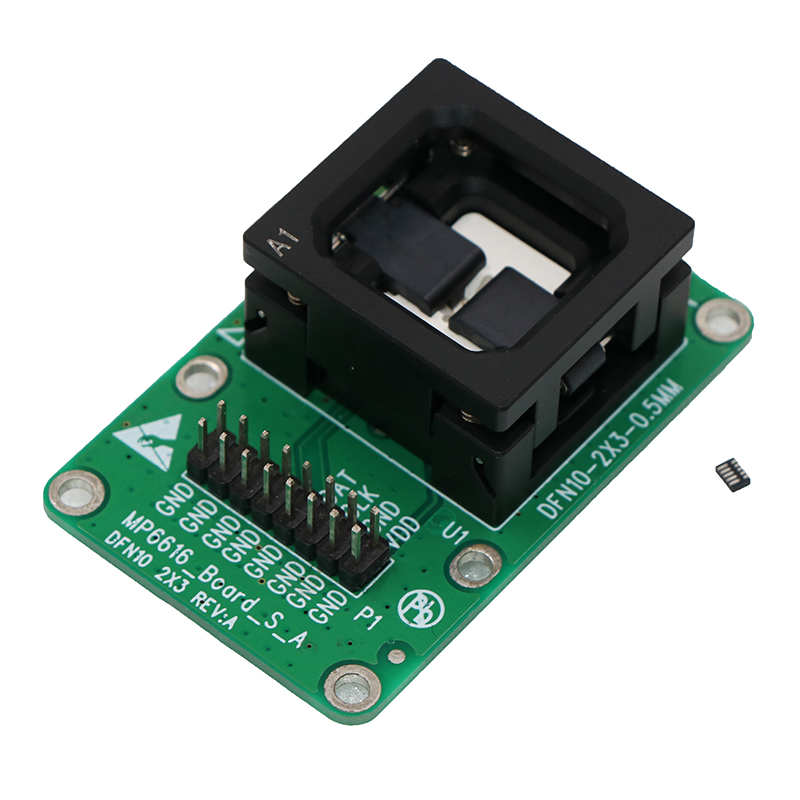
3. Contact Reliability
- Pad Design: The size and shape of pads on the PCB must match the contacts of the test socket. Larger pads can provide better contact area, increasing the stability of the connection to the test socket.
- Surface Treatment: Using high-quality surface treatment processes (such as gold plating, HASL, etc.) can improve the wear resistance and conductivity of pads, reducing oxidation and ensuring reliable electrical connections during each test.
- Good Hard Gold Pad for Pogo Pin Contact: Pogo Pin and Spring pin with surface mounting have strong pressure on PCB pads, because pins are spike or sharp tip.With insert many times,Socket pins will press the PCB pads same times, so the Pads strongth must be good.
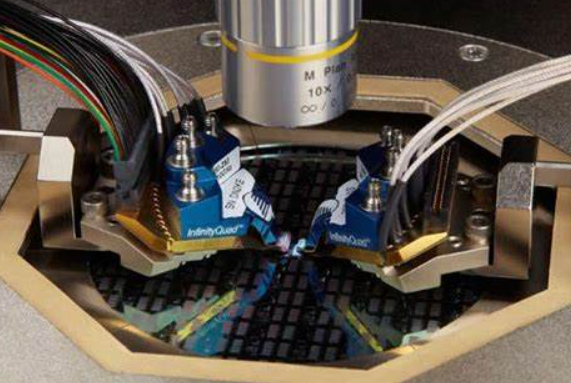
4. Thermal Management
- Heat Dissipation Design: During testing, certain components may generate significant heat. A well-designed PCB layout can effectively disperse heat, preventing damage to components or inaccurate test results due to overheating.
- Positioning of Heat-sensitive Components: Placing heat-sensitive components in suitable locations, combined with effective PCB heat dissipation designs, can ensure that testing does not adversely affect the normal operation of other components.

5. Compatibility
- Matching Test Socket Design with PCB Layout: The design of the test socket needs to complement the PCB layout, and an optimized PCB design can adjust component positions based on testing needs, ensuring smooth integration with the test socket.
- Reusability: A good PCB design allows the same test socket to be used for different versions of circuit boards, reducing development and maintenance costs for testing equipment.
6. Cost-effectiveness
- Reducing Defect Rates: High-quality PCB processes can lower defect rates during production, minimizing rework and maintenance costs due to failures, thus saving costs in the long term.
- Improving Production Efficiency: Optimized PCB processes can enhance production efficiency, shorten production cycles, and ensure timely delivery of testing equipment, strengthening market competitiveness.
Conclusion
In summary, PCB processes play a crucial role in the performance, reliability, and cost-effectiveness of test sockets. By ensuring signal integrity, mechanical stability, contact reliability, thermal management, compatibility, and cost-effectiveness, the efficiency and accuracy of the testing process can be significantly improved, ultimately enhancing the overall quality of products and their competitiveness in the market.
发表回复